1、空分装置一液位自动控制系统,液位测量采用差压变送器、DCS和气动薄膜调节阀构成调节系统,开车初期,投自动液位波动很大,无法满足生产要求
故障检查、分析:开车初期,由于系统冷量未达到平衡,同时液位导压管内冷热不均,造成导压管内气液混合,且测量值本身波动很大,投入自调后,更加重了波动。
故障处理:首先打至手动状态,手动控制,对液位差变进行排表处理,对正负导压管从塔壁排至挂霜后,开表。待手动稳定一段时间以后,投入自动。经过以上处理之后,基本可以达到工艺要求,使波动较小。
2、有一简单控制系统,控制器的偏差、控制器的输出均正常,但有偏差时PID调节器仍然按照原控制规律动作,而被调参数仍不回给定值,有时向反向动作
故障检查、分析:从故障现象看,系统中的测量部分、控制部分及信号传递无问题,故障可能在调节阀部分(阀杆位移、膜头堵塞、阀门定位器故障)或PID调节器输出到阀门定位器的传递信号线部分。检查PID调节器输出信号至调节阀间线路正常,检査调节阀膜头时发现膜头接头气路被砂粒堵塞,导致控制器不能正常工作。
故障处理:疏通后,系统恢复正常。
3、有一中压蒸汽压力是靠PV108放空来控制的简单控制系统,某日,操作工发现压力降低,PID调节器输出阀位正确,但是偏差消除不了
故障检查、分析:从故障现象看,PID调节器输出到安保器无问题,可能是安保器输出到阀门定位器、调节阀问题。先检查阀门定位器及调节阀,均无问题,再用万用表量安保器输出信号,结果无输出。
故障处理:更换输出安保器,系统即恢复正常。
4、某装置一简单控制控制回路(DCS控制系统,PID控制器),在投入自动后,控制器无动作
故障检查、分析:引起控制器不动作的原因可能是:DCS组态是否有问题、控制器自调参数是否正确。检查DCS组态全部正确,但检查控制器P、I、D参数时发现不正确。
故障处理:将PID参数整定正确设置后,投用正常。
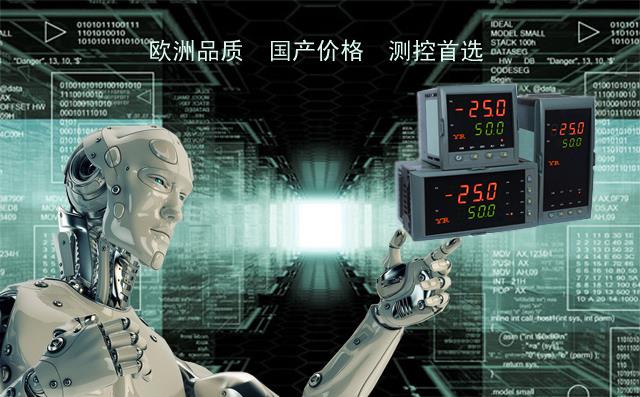
YR-GAD系列人工智能控制器
5、横河DCS系统单回路,产生OOP故障报警
故障分析:OOP表示输入开路,可能是变送器线断或者是变送器输入信号低于4mA或大于20mA。
6、横河DCS系统单回路,产生OOP
故障分析;OOP代表输出开路,可能是接线松动所致。
7、有一个单回路控制系统,投自动时经过长时间整定仍无法稳定投用,利用给定值加干扰后有回调趋势,并且调节周期和调节幅度正常,可是无法稳定
故障分析:从故障现象看,这个系统的整定参数是合适的,无法稳定的原因不在参数上。
故障处理:重新分析回路正确设定PID调节器的正反作用,使系统达到负反馈,投用后正常。
8、有一个控制回路从开车正常投用使用多年,正艺条件未变化,控制效果越来越差
故障检查、分析:原来能正常投用说明参数正常,效果逐渐变差说明有渐变条件影响控制。检查调节阀时,发现阀芯冲蚀严重。
故障处理:阀修复后投用正常。
9、DCS系统中一控制回路,原来一直正常使用,后因输点通道坏,将AO点通道更换后,无法控制现场阀开度
故障检查、分析:因为换过通道引起故障,所以从改动处入手分析问题。因为AO卡通道更换过,并且重新下装,控制点找不到原先的通道,所以不能控制。
故障处理:将对应的控制点重新下装后,可以正常控制。
10、一锅炉汽包液位控制系统原来正常投用,突然出现较大的波动,打到手动控制,液位波动
故障检查、分析:从故障现象说明工艺操作条件已经和原来投用的条件不一样了,需要重新整定参数。
故障处理:经过加大控制强度,克服干扰波动后正常。
11、某塔液位控制是单回路控制系统,在负荷调整的过程中发现液位不稳定,波动较大
故障检查、分析:检查发现液位调节阀LV0405阀开度只有7%,阀位不断变化,调节阀在小开度下易产生喘振,定位器输出不稳,因此调节阀不稳。
故障处理:将调节阀打开到15%以后调节阀恢复正常,但过量大无法保证液面,使用前后手阀限量才保证了正常控制。
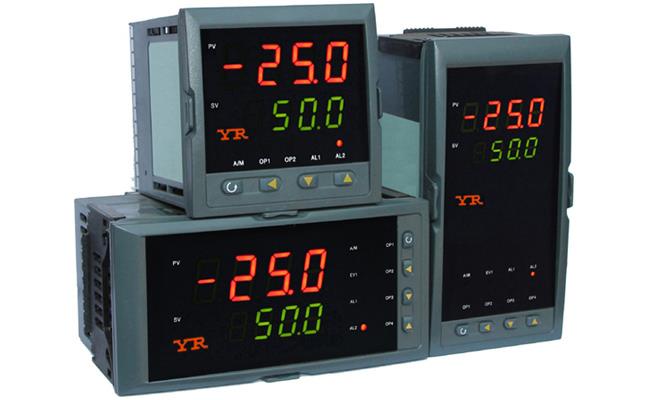
人工智能调节器YR-GAD系列
12、某石化装置一液位单回路控制系统,由于负荷降低,LV402阀开度只有5%,结果产生了振动,液位不稳
故障分析:调节阀在小开度下极易产生振动,振动时就影响阀门定位器振动,输出不稳,因此自调不稳。
故障处理:将前或后截止阀稍关小一些,限一部分流量,到阀位开到15%时,振动消失,阀门定位器也稳定了,投自动运行正常。
13、一液位简单控制系统(DCS系统PID控制器,调节阀为气开调节阀)无法投入自动控制
故障检查、分析:引起无法投入自动的主要原因是:控制器参数不当、控制对象问题或调节阀有问题,检査上述处个故障点,在对调节阀检查时发现,调节阀内漏量很大,调节阀只要有小开度,就有很大的流量。
故障处理:对调节阀内件进行处理后,问题消失。
14、蒸汽压力控制系统的故障一例
a、无纸记录仪上蒸汽管路压力记录值突然降到零,而安全阀起跳,为仪表原因。在引压管与记录仪表之间出现故障时,调节阀开度突变,引起蒸汽压力猛增,而无纸记录仪却无反应,此时可先切到手动遥控调节阀,再处理故障。
b、无纸记录仪上蒸汽管路压力记录值未高于设定值,安全阀即起跳,仪表人员可以对照相关仪表,如各点温度正常,则安全阀未调好;如各点温度值升高,则为压力记录值低于真实压力。
c、压力波动虽大,但缓慢,一般应从工艺上查找原因。
d、压力波动呈快速振动状态要从参数整定及仪表本身查找原因。
e、如负荷、加料回流、温度等变化以及操作不当,均会引起设备内部压力的变化,要从工艺操作上找原因。
f、对每台仪表的平时压力波动情况应心中有数,分清是异常情况还是正常情况,并可参照其他工艺参数作出判断。
15、液位控制系统故障一例
a、在光柱调节器上显示液位值跑向最大或最小,可先对照一次表。如一次表正常,则为二次表故障。如一、二仪表一致,则手控调节阀检查液面有无变化。有变化一般为工艺原因,如无变化一般为仪表问题。
b、带负迁移的仪表示值跑向最大,应怀疑负压侧泄漏。有气相压直接引到负压侧的仪表示值跑向最小,应怀疑负压侧集液罐液体上升过高。
c、记录示值波动频率高,一般可能是参数整定不当或一次仪表振荡等原因所致。如波动缓慢,一般为工况原因。
d、如怀疑仪表为假液位指示,一般可将系统切到手动,工艺、仪表人员共同用校准压力表测出气相压力进行分析。
16、温度系统故障一例。
某装置一重油温度控制系统,重油通过热交换器,采用蒸汽加热,改变蒸汽调节阀开度,重油温度变化缓慢,投到自动控制时温度大幅波动
故障分析:改变蒸汽流量、重油温度不能明显变化,说明检测系统有滞后,检查热电偶测量系统,确认没有问题,说明传热系统可能有问题。为了充分利用蒸汽潜热,中压蒸汽要冷凝成水后再通过疏水器定时排放掉。蒸汽和重油通过热交换器进行传热,热交换过程需要一定时间。中压蒸汽温度280℃,加热后重油为150℃,当加热蒸汽温度由280℃逐渐冷却,与热交换后的重油温度150℃相接近时,热交换几乎达到相对平衡(由于热阻存在,有一点温差),此时加热蒸汽尚未全部冷凝成液体,它仍占据着热交换器的空间,即使开大调节阀,新的蒸汽也补充不进来,即便补充也是微量。这样造成用于热交换的蒸汽温度达不到设计值280℃(虽然外来蒸汽温度是280℃),而是在280℃与蒸汽冷凝成水的温度之间变化。由于实际用于热交换的蒸汽温度低于设计值,热交换时间增加,造成温度测量滞后,测量滞后大就造成系统不稳定。
故障处理:针对该系统,整定智能温控器PID参数,:增加微分作用,加适量的积分作用,加大比例作用,P=50%,Ti=5min,Td≈1.5min,结果比较理想。