为什么要分工呢?因为现代化企业对专业知识要求很深、且差别很远。比如,在钢铁企业,从事用户服务和产品开发的,往往是材料专业的;而搞工艺的则是冶炼或轧钢专业的;搞控制的是自动化专业的;搞信息系统的往往是计算机专业的;搞设备的是电气或者机械专业的。
技术人员的工作,都是通过自己的“手段”来实现自己的“目标”。专业间的合作方式一般是这样的:一个专业向另外一个专业提出要求。也就是说:一个专业的手段,是另一个专业的目标。
比如,用户服务的目标是:研究产品达到什么样的质量指标,才能满足用户需求。这时,他的手段就是产品的质量指标,目标是满足用户的具体工作需求。他的这个手段(也就是质量指标)会传递到产品研发工程师那里。所以,搞产品设计的人需要研究:各个生产工序要达到什么样的工艺要求,才能达到上述质量指标。这样,接力棒就传到了搞工艺的人手里。搞工艺的要知道:工艺参数如何设定,这个工序才能符合要求。而搞设备和控制的,则是通过设备的维护、控制方法的实时,来达到工艺人员提出的要求。
在要求的传递过程中,会出现一些矛盾。比如,工艺人员希望温度控制波在10度以内。但受现实条件的约束,在控制过程中可能是无法实现的。这时候,就可能要改变工艺、乃至产品设计方式,才能实现。还好,这种矛盾一般发生在产品研发阶段。研发结束后,一定会找到一种可行的做法。人们会把这种做法固定下来,形成标准,此后照此执行。这时,才进入大生产阶段。所以,现代化企业的大生产阶段,是按照特定的标准体系进行的。有了标准,不同专业之间的关系就解耦了:各自达到各自的目标,就可以了。这样,分工也就容易实施了。
但糟糕的是:生产过程不可能一直是稳定的。总会出现这样的或者那样的问题。比如,生产速度或节奏的变化、设备状态的变化、原料或者操作的变化、原料特性的偏移、甚至包括用户需求的变化等。这个时候怎么办呢?如果严格执行标准,则成本会剧烈上升、收得率和生产效率剧烈下降;如果不严格执行标准,则难以生产高质量的产品。如果企业对质量、成本的要求不是很严格,问题往往是可以容忍的;如果市场对质量和成本的要求越来越高,问题就变得无法容忍了。如果产品体系复杂多样,问题就更加严峻。
面对这样的矛盾,合适的做法就是“以变应变”。这时候,就出现了IT与OT融合问题。
举个例子。过去,工艺要求控制到某个温度的目标值(标准的要求)。现在,由于前工序发生了变化,就需要改变这个目标值。目标值应该怎么定呢?要根据产品要求重新制定。如前所述,产品要求的目标值,往往是研发阶段试验摸索出来的结果。在大生产阶段需要立刻改变目标值;这时,就必须有数学模型才能支撑。这个模型要把产品和工艺知识通过数字化模型的办法融合起来。
现实中,可能还会发生更为“严重”的问题:某工序的一个问题,可能导致无法在下工序制造出符合特定用户要求的产品。这时,就要把这个“半成品”转用到其他用户那里(用户不同,对产品质量要求不一样)。这时,工艺要求、控制要求就会实时地发生发生系列化的变化。要实现这种变化,就需要几乎所有专业的知识融合、知识数字化了。
我们要理解标准和模型的关系:IT与OT融合是需要模型的。因为只有模型,才能做到实时地改变“标准”。但是,即便如此,工厂仍然是按照“标准”组织生产,只是“标准”用模型的形式来固化了。这时,对标准的管理,也会面临新的挑战。
作者:郭朝晖(工学博士,教授级高工。企业研发一线工作20年)
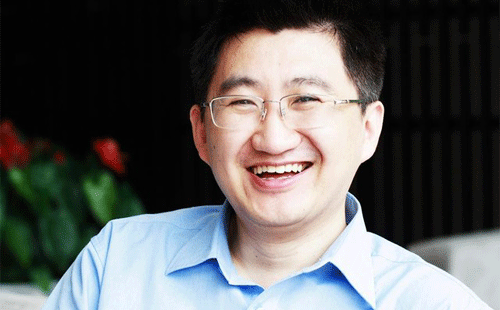
相关阅读
IoT大潮下一个IT人眼中的OT