出铁秤(车载秤)
在炼钢厂,无论是采用混铁炉出铁方式还是采用鱼雷罐出铁方式,都要用到铁水车车载秤,也称为出铁秤,它是这个区域最重要的一个仪表设备,也是自动化炼钢的基础。尽管有经验的出铁操作人员可以根据铁水包壁的渣线出铁,但往往是每个包的耐火材料侵蚀情况并不一致,很可能每次带来5-10t的波动,这对于自动炼钢模型就是很大的影响了。一般从这里出来的铁水净重直接进入转炉的12自动炼钢模型,采用自动化炼钢的钢厂很少有在输入界面预留人工设定窗口的,如果不能及时输入这一净重值,炼钢生产就会面临停产的危险。
济南金钟衡器等国内企业在铁水车设计、制造方面有较为成熟的经验,车载秤的设计成熟,车载秤应用技术处于领先水平。下面以此为例介绍一种比较可靠的铁水车车载秤设计。
通常工称120t转炉的铁水的装入量为140t左右,废钢的装入量为20-26t,估计总装入量为160-170t,出钢量在152-160t左右。考虑到配套的铁包重量(65t)及正常情况下载重包(约210t)起落的冲击也在允许范围之内。这样在设计选型时,一般选择四个100t的称重传感器分置在铁水车的两侧,如图1所示。
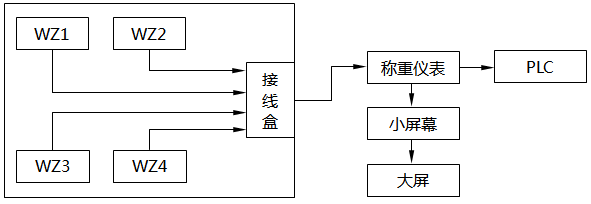
图1 炼钢厂铁水称量车俯视图
图1中给出了一个以申克称重传感器和飞利浦显示表搭配的实例框图。考虑到100t申克称重传感器价格昂贵(约10万元),也有不少设计和使用部门开始釆用余姚通用仪表厂、北京701研究所等国内有实力的传感器制造厂家的产品,实际效果也不错。现有的设计,基本满足了生产的需求,但从现场使用来看,还有改进的空间。因为对称重仪表传感器保护程度不够,以致造成整台地车无法使用的事例还是较为常见。例如,铁水车上的铁包经常一次出铁不能装满一包,需要长时间停在车上等待。如果没有冷却措施,铁包的温度会把称重传感器和信号传输电缆烫坏,影响正常出铁。因此,设计时需要重点考虑这个看似不重要的问题,在制造时配置冷却风管,到现场安装时再连接一根金属软管,通上压缩空气。金属软管不需要卷筒拖动,可以落在地面上或者悬在空中随车运动,一般情况下不会磨坏。压缩空气可以保证称重传感器内的温度不超过允许工作范围。
炼钢厂出铁秤常见故障
出铁秤与出钢秤类似,都属车载秤,是大型钢铁企业常用的计量衡器。它经常安装在炼钢车间的转炉前,用来称量转炉入炉的铁水。由于受到所处环境的限制,出铁秤常会出现一些故障。怎样快速排除故障,尽快恢复生产,是衡器技术人员面临的共同课题。
常见故障之一:拉线、烧线、短路使传感器及仪表烧坏。
炼钢厂出铁秤故障原因及部位
1、用于称量铁水的车载铁包电子秤一般安装在混铁炉下面几米深的基坑中,有轨道可来回行进,当启动车速过快时易拉断称重传感器总线。
2、出铁时,铁水四溅,如果传感器线缆无良好的防高温物质包裹,很容易把称重传感器总线及各支线烧毁。
3、当车载出铁秤的电动机线与称重传感器各线同时烧成裸线时,电流可进入传感器及仪表内,称重传感器及仪表一同烧坏。
炼钢厂出铁秤拉线、烧线、短路使称重传感器及仪表烧坏故障防止措施及解决办法
1、加强对现场人员的管理,使其对车体行程的距离长短、车速快慢有一定掌握。
2、电动机线与称重传感器总线应分别安装在车载秤体两侧。
3、为了防止电流进入称重传感器及仪表,在称重传感器总线处接一个保险装置。
4、称重传感器总线及电动机线上各自串上电瓷管,外加蛇形金属管,并用石棉布包裏,这样就能非常有效地防止跑铁、漏铁时烧线及烧坏传感器。
常见故障之二:仪表显示称量包的重量与实际包重量误差过大。
故障原因及部位:
1、秤体下的轨道杂物太多,轨道不平,影响称量的准确性。
2、当天车工放铁包时,容易造成偏载现象。
3、秤体四个角的某一个或几个称重传感器有故障。
防止措施及解决办法:
1、当装铁有铁料落入基坑的轨道上时,需有专人清理坑内轨道旁的杂物,以保证秤体平稳,增强秤体的准确度。
2、当天车工放包时,秤体旁需安排专人指挥,以防止偏载发生。
3、当排除上面两种原因后,而称重传感器总线、各支线没问题时,应考虑是否是传感器损坏。此时应打开接线盒,将四个称重传感器中三条桥路的电位器线断开,留一个不动,用标准砥码去压保留传感器的秤体一角,记下数值,然后顺时针或逆时针逐一如上试法,通过记下的数值 就会知道哪个传感器有故障。也可以通过将测量阻值与初始值做一个比较,就可以知道哪个称重传感器有故障。
从现场来看,由于岀铁时铁水、渣子等高温液体的烫伤和反复运动对电缆的拉伸与折叠,信号传输电缆是最容易出问题的部位,这时最好的办法就是更换电缆。换电缆也很有讲究,首先建议选用KVVRP 6×1.5带颜色的耐高温电缆,可以短时间避免一般的高温烫伤,但很难保证能够经受不停地来回反复的拉伸与折叠。如果有条件,可以直接选用拖链专用电缆,要比一般电缆耐用很多。每根芯子上最好带有不同的颜色,以便现场直接按照颜色对接。否则在线号印刷不清和现场倒罐坑昏暗的照明条件下,很容易接错线,既难以发现,又影响生产。
其次,最容易出问题的部位是称重传感器,这是因为有时铁水不足,不能一次出满一包铁,为了等铁水,半包铁水长时间(超过30min)放在秤上,即使在传感器周围通了冷却风也很难避免称重传感器不被烫坏。有的传感器的耐温上限为752,但时间长了传感器的阻值特性也会发生改变,造成出铁时铁水重量无规律波动,这时只能更换传感器。经济一些的办法是通过测量判断哪个称重传感器信号不稳,就更换信号不稳的那个传感器;更好的办法是同时更换4个,然后对下线的传感器送修。
除此之外,接线盒也会出现问题。接线盒平均一年出现两次问题,注意及时更换就可以了。由于设计一般选用申克公司的产品,价格大约在3000多元,也有不少厂家开始选择国产化的产品,因为两者在原理上是一致的,都是基于惠更斯电桥的平衡原理。
出铁秤的校准与数据传递
现场常用的校验方法是实物标定法,即先准备一个已经在更高一级计量秤上称好的实物包,重量与实际出铁重量接近,然后以此为准分别校验零点和量程。有时为了提高校验的精度,在两者中间设置一个中等重量的实物砥码,以便确保秤的线性;不过,现在的称重传感器制造技术已经很高,线性一般都比较好,可以忽略。但是,为了保证校准的可靠,建议还是按照计量程序进行。
首先进行空秤校准:将显示仪表通上电源,预热30min,使衡器保持空秤状态。将后面的 拨动开关“CAL”拨向C位置解锁,然后同时按下B+T键进入设置状态进行设置。按下ENTER键,比如显示最大量程“230000”。按下ENTER键,提示进行空秤校准。保持空秤稳定,按下ENTER键,即完成空秤校准。按下TARE键,将后面拨动开关“CAL”拨回中间位置, 返回称重状态。
第二再做称量校准:将铁水车开至装包区,然后执行带载校准。将标准包吊至铁水车上。键入标准包重量,按下ENTER键,将铁水车开至校验区,观察数值是否波动。如正常,重新进行一遍空秤校准,然后将后面开关“CAL”拨回中间位置,返回称重状态。计算△=A-B,式中,A为称重显示值,kg;B为标准值,kg。
若△max的绝对值不大于允差的绝对值,判为合格,出具校准证书和原始记录,否则应检修调整,仍不合格者则禁用。铁水秤的校准周期一般为6个月。
现代大型冶金企业在自动化控制系统设计时,一般按照L1、L2、L3的模式进行配置。L1是基础自动化级,负责收集现场传感器来的信号,控制现场元件;L2是过程控制级,负责生产模型运算等;L3是管理级,负责计划的下达。铁水重量信号一般参与L1、L2的控制,为了把从鱼雷罐到倒罐坑仪表显示的净重传到LI、L2网络中,可以通过PLC传递到转炉服务器, 现场一般设置2台秤,可以共用一套PLC。
如果现场的出铁秤不止一台,编程时需要分别定义不同的PLC的IP地址和内部寄存器地址。通过称重仪表的4-20mA输出送到PLC输入模块。例如,1号坑,IP地址为172.17.48.83,寄存器地址:实型数(REAL)、400012双整型(DINT)、400016整型(INT)400018;2号坑,IP地址为172.17.48.82,寄存器地址:实型数(REAL)400012、双整型(DINT)400016、整型(INT)400018。同类企业可以参照类似定义方法配置。