热电偶套管套在热电偶元件外面,用来抵御被测介质的压力和腐蚀。为测量汽轮机内部蒸汽的温度,通常将热电偶套管伸入汽缸内部进行测量,以取得较为准确的数值。但由于汽缸内蒸汽压强大、流速快,热电偶套管处于极恶劣的工况下,因此经常发生损坏,这不仅会导致温度信号丢失,严重时甚至会危及汽轮机设备的安全运行。本文将分析汽轮机热电偶套管损坏的原因,并对热电偶套管的改进措施进行探讨,这对同类型汽轮机机组热电偶套管的改造工作具有指导意义。
1、设备介绍
某电厂1台600MW汽轮机机组(厂内编号6号机)为国产引进型高中压合缸、单轴四缸四排汽凝汽式机组。由安装在高压外缸上半部分左侧、右侧的2支热电偶元件来测量调节级蒸汽温度,其热电偶套管伸入缸内直至调节级动叶后面。由于高压缸采用双层缸结构,调节级蒸汽热电偶保护套管设计成双层保护套管形式,俗称内外套管。其中,外套管固定在高压内缸上,并伸至隔板套内调节级动叶后。内套管则固定在外缸上,并伸入外套管内,两套管轴向保留6.5mm的膨胀间隙。
2、故障现象
近日6号机组运行负荷350MW,主蒸汽温度537℃、压强13MPa,再热蒸汽温度536℃、压强1.79MPa,凝汽器真空A侧压强98kPa,B侧压强99kPa,机组各轴瓦(包括推力轴瓦)温度、振动均显示正常,润滑油油温正常,主机轴向位移+0.27mm,正常。时间:19:21:33,6号机组汽轮机跳闸,锅炉MFT,跳闸原因显示为汽轮机轴向位移超过ETS主机位移保护跳机值(+1.0mm/-1.0mm)。停机过程中,汽轮机缸体、轴封、轴瓦没有明显异声。事后检查6号机组运行参数历史曲线,发现汽轮机跳闸前,时间:19:21:33主机轴向位移由+0.25mm逐渐减小,时间:19:22:03,2号轴瓦振动瞬时突升至X向97.42μm,Y向89.56μm后回落。时间:19:22:54,轴向位移从-0.22mm瞬间大幅变化,最大至-1.85mm。时间:19:23:02,6号机组汽轮机跳闸,此时轴向位移又瞬时变化至+0.25mm。时间:19:23:15,推力轴瓦非工作面瓦块温度最高升至123.9℃。根据运行参数的变化,初步断定汽轮机通流部分发生故障,造成了转子推力异常变化,推力轴瓦非工作面瓦块磨损,因此申请机组调停检查。停机后,对高压缸解体检查,发现有下文所述的缺陷。
2.1 调节级蒸汽热电偶保护套管严重损坏
解体后发现左侧(从机头往机尾看)内、外套管都已完全断裂脱落,内套管掉落在内外缸之间,外套管掉落在高压内缸测温孔内。右侧内外套管头部也已损坏,发生了折断现象。断裂情况如图1-图3所示。
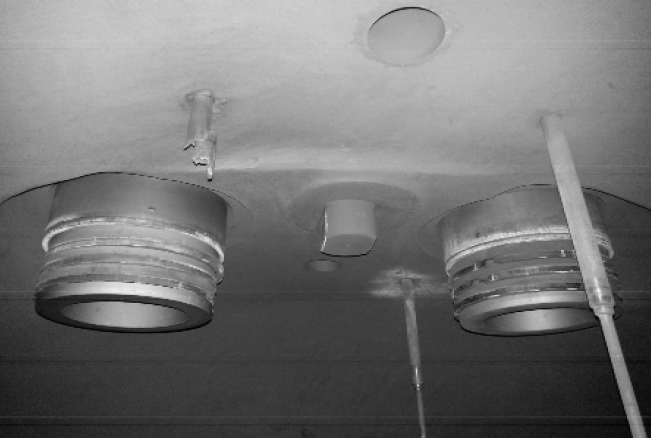
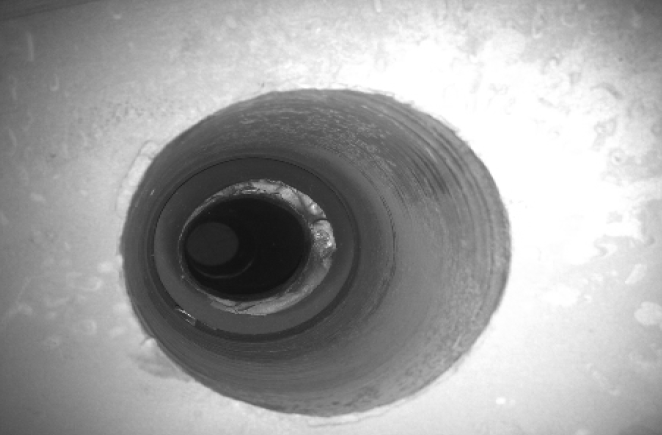
图2 左侧外套管断裂
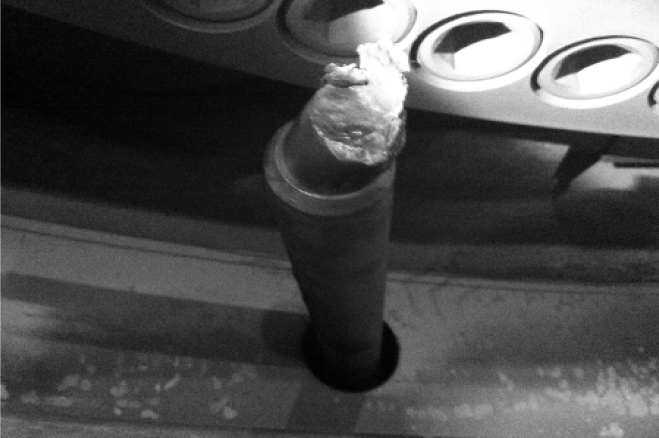
图3 右侧套管断裂
2.2 调节级动叶出汽边严重变形
检查还发现所有调节级动叶片出汽边均发生严重变形,如图4所示。每片叶片的出汽边背弧面向内凹陷变形严重,叶片的叶顶、叶根处甚至出现了开裂,背弧面的出汽边均有刮擦的痕迹。从调节级蒸汽热电偶套管的位置来看,右侧套管发生弯折后很有可能撞击调节级动叶,且在转子顺时针旋转时,连续撞击叶片从而导致如此变形。
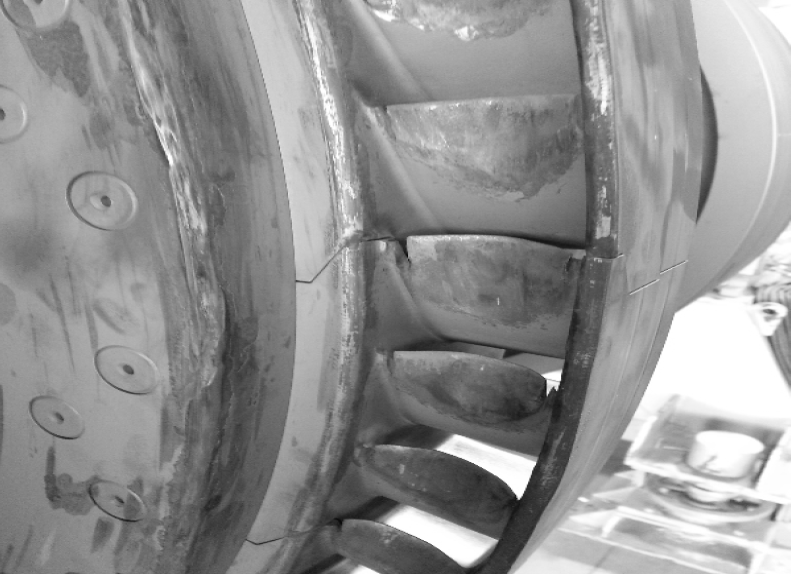
图4 汽轮机调节级叶片损坏
2.3 推力轴瓦非工作面瓦块完全磨损
解体推力轴瓦,发现非工作面(机头侧)瓦块表面钨金全部磨损熔化,瓦块见基材,而工作面瓦块未发现异常。检查转子推力盘,有清楚的整圈摩擦痕迹,但没有沟槽、划痕等缺陷。
3、原因分析
3.1 汽轮机故障过程分析
结合机组故障时运行现象发生的时间顺序及高压缸解体情况分析,得出以下结论:此次汽轮机故障的过程是调节级蒸汽热电偶套管发生脱落后撞击调节级动叶,导致整圈动叶严重变形,调节级汽流通道面积明显减小,使得轴系反向推力大幅增大,造成推力轴瓦非工作面瓦块过载,钨金磨损,转子轴向位移超过了机组跳闸保护值。
查阅调节级蒸汽左、右2支温度测点历史数据可知,左侧热电偶数据在此次汽轮机故障前早已失去,即左侧内外套管早已发生损坏,而右侧热电偶数据正是在这次故障时失去的,证明右侧热电偶套管是被左侧套管脱落的残骸撞击头部后发生弯折的,随后其与高速旋转的调节级动叶发生撞击。
3.2 热电偶套管脱落原因
从图2可知,左侧外套管断面内孔呈椭圆形,断口截面各处宽度差别明显,由此可确认左侧外套管运行中内壁受到了长期的单侧磨损,局部管壁由此减薄。此外,断口位于套管变径处,断口以上套管部分与高压内缸测温孔成0.05mm的过盈配合,断口以下部分则有一定间隙,所以形成了所谓“悬臂梁”结构,蒸汽流对伸入高压隔板套内的那段套管表面的冲刷力是不平稳的,在套管变径断口处产生极大的交变应力,再加上此处管壁减薄,最终发生断裂、脱落。随后,内套管在失去外套管的保护后受到高压汽流的冲刷,因为内套管强度远不及外套管,且内套管伸入高压内缸以下的部分同样也是悬臂梁结构,所以内套管也发生折断、脱落。脱落的内外套管残骸落在调节级后的隔板套内,受汽流的冲刷,和周围的高压转子、高压隔板套、高压第1级静叶发生了杂乱无章的撞击,期间撞击右侧外套管,使其头部发生朝调节级动叶方向的弯折,并与调节级动叶发生撞击。左侧外套管内壁长期受到碰磨的主要原因是内、外套管安装不同心。我们可以排除内外缸体的相互移动或者套管、缸体测温孔尺寸不正确等影响因素,剩余最有可能的原因是内外缸测温孔在基建加工时就存在不同心,这可能与测温孔中心定位方法和钻孔的准确度不够有关。
4、改进措施及探讨
针对调节级热电偶套管易断裂脱落的问题,提出了以下几种改进措施。
4.1 控制缸体测温孔加工质量
对于新加工的机组,严格控制加工质量。工艺上将各缸体测温孔从单独加工改为总装时号钻,从而从根本上避免出现各缸体相同测温孔不同心的问题,同时,所有热电偶套管在总装时进行试装配,不把问题遗留在现场。
该措施不仅从工艺上对缸体测温孔开孔进行了规范,而且强调其在制造厂总装时进行,以制造厂较高的加工质量来保证新机组缸体测温孔加工的准确性,与电厂现场加工相比,质量上更有保证,但不能完全避免热电偶套管再次发生脱落。
4.2 高压隔板套上增加热电偶保护套
在高压隔板套测温孔上加工出螺纹,然后将另外加工好的保护套安装在螺纹孔上,并焊接。
该措施最大的优点是即使调节级热电偶套管发生断裂,也不会脱落撞击到汽轮机叶片,但隔板套测温孔上螺纹加工困难,同时多出的一层保护套管降低了调节级蒸汽温度测量的准确性。
4.3 调节级热电偶双层套管改为单挠性套管
将调节级蒸汽热电偶套管由原先的双层刚性保护套管改为单挠性套管,但套管不穿透高压内缸,内缸上的测温盲孔的孔底距缸体内壁保留10.5mm的厚度,这样保证了调节级后蒸汽不会通过内缸测温孔泄漏。套管上段有一波纹节和一片法兰,与热电偶整体加工而成。单挠性套管安装时通过法兰与另一片焊接在高压外缸上的法兰进行连接固定。
首先,该措施简化了调节级热电偶套管的结构形式,减少了套管安装环节,避免了双层套管之间因安装不同心产生碰磨的问题,使保护套管损坏率下降。其次,高压内缸测温孔为盲孔,可完全防止套管发生脱落后撞击到汽轮机叶片,比在高压隔板套上加装保护套管更可靠。第三,有分析指出,共振是热电偶套管断裂的主要原因,套管上的波纹节可改变套管固有的振动频率,避免发生共振,防止保护套管损坏。第四,虽然单挠性套管未直接接触到调节级后蒸汽,温度测量的准确性受到影响,但是单层保护套管能够比双层套管更准确地测量温度,因此二者因素相互抵消,单挠性套管对测量准确性的负面影响有限。
5、结论
调节级蒸汽热电偶双层保护套管的结构形式以及高压内外缸测温孔加工的不同心是导致热电偶套管碰磨损坏脱落,进而撞击汽轮机叶片的主要原因。它始终是影响汽轮机安全运行的隐患。事实证明,调节级热电偶套管的脱落会对汽轮机造成严重损坏。本文通过比较认为,调节级蒸汽热电偶套管由双层保护套管改为单个挠性套管(内缸测温孔为盲孔)具有诸多优点,是最为安全可靠的方案。由此证明,为了彻底排除隐患,应采取恰当的改进措施,这对汽轮机的安全运行有着十分重要的意义。
《热电偶套管脱落致汽轮机故障的原因分析及改进措施》作者:浙江浙能嘉华发电有限公司 韩亮,1974年出生,男,毕业于武汉水利电力大学,本科,工程师,从事电厂汽轮机设备检修维护管理工作。